Crane LTR Liner Panel
Product
Kemlite® Embossed Liner, LTR, is a lightweight and durable fiberglass reinforced plastic (frp) panel. It is more cleanable, more stain resistant, and more abrasion resistant than competitive frp panels. Kemlite® is comprised of random chopped fiberglass and polyester resin.
Purpose
Kemlite® Embossed Liner, LTR, is specifically designed and formulated for use as a sidewall liner, ceiling liner, scuffplate panel, or subpan for refrigerated and dry van trailers, truck bodies, seagoing containers, and rail cars.
Composition
Reinforcement: Random chopped fiberglass. Resin Mix: Modified polyester copolymer, inorganic fillers, and pigments.
Finished Panel Quality
The frontside of the panel shall have a pebble-like embossed finish. The backside of the panel shall have a smooth finish.
The backside surface may have some variations which do not affect functional properties and are not cause for rejection. The backside of the panel is comprised of a polyester copolymer surface that is commonly bonded with adhesives or to foam in lamination processes. Typically, no additional preparation is required as long as the surface is dirt and oil free.
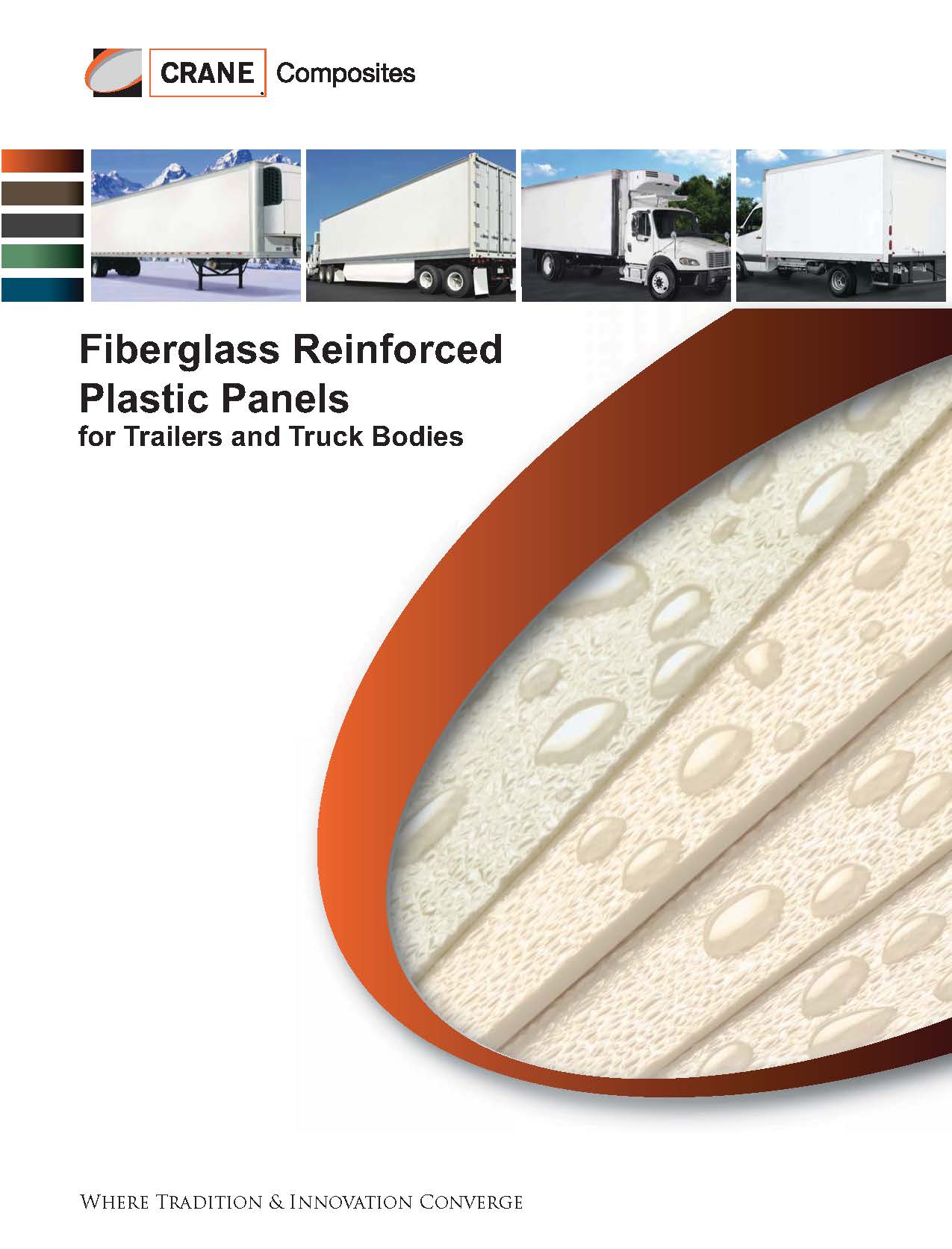
Download Brochure
Certifications
1. Meets USDA/FSIS requirements. Reference document #6776 for conformance statement.
2. Meets FMVSS 302 requirements.
Note: Protect your eyes with goggles; cover your nose and mouth with a filter mask; cover exposed skin when cutting CCI panels.
HAND FABRICATING: Drilling—High speed drill bit (60° cutting angle, with 12°-15° clearance) or hole saw.
STAPLING: Standard pneumatic stapler.
CUTTING: Sheet metal shears or circular saw with reinforced carborundum or carbide-tipped blade.
PRODUCTION FABRICATING: Use carbide-tipped tools. Straight cuts can be sheared (90° cutting edge with 0.002″ [0.05 mm] clearance) or sawed. For irregular cuts, use die punch or band saw.
PAINTING PREPARATION: You should always test and validate the selected paint system with the frp panel prior to application.
To properly prepare the panel surface for painting, make sure the surface is clean, dry, and free from all oils, grease, silicones, dust, and other contaminants. Common practices for preparation before painting include using alkaline detergents or clean water. Sanding or roughening of the panel surface is recommended to promote paint adhesion. 600 grit or finer sand paper or a 3M “Ultrafine”
Scotch-Brite® pad are commonly used to roughen the surface.
Design Data Notes
Bulk coil may be ordered in long lengths or in specific cut-tosize pieces. Standard coil sizes are 250′ and 500′, custom sizes are available. Crane Composites reserves the right to manufacture and ship total linear footage of long length bulk coils ordered within the following parameter lengths per piece:
Min. 200′ | 61.0 m
Max. 550′ | 167.6 m | Liner w/ Integral Scuff –
Liner 0.090″/ Scuff 0.120″
600′ | 182.9 m | Liner & Liner/Scuff – 0.090″ & 0.120″
700′ | 210 m | Ceiling – 0.075″
800′ | 243.8 m | Ceiling & Subpan – 0.060″
2. Cut-to-size lengths 12′ (3.7 m) and over of the same width
will be interlapped (18″-36″ [457.2 mm-914.4 mm] interlap
per panel) into a coil for ease of handling and shipping. Total
length tolerance – 0″ and +6″ (-0 mm and +152.4 mm)
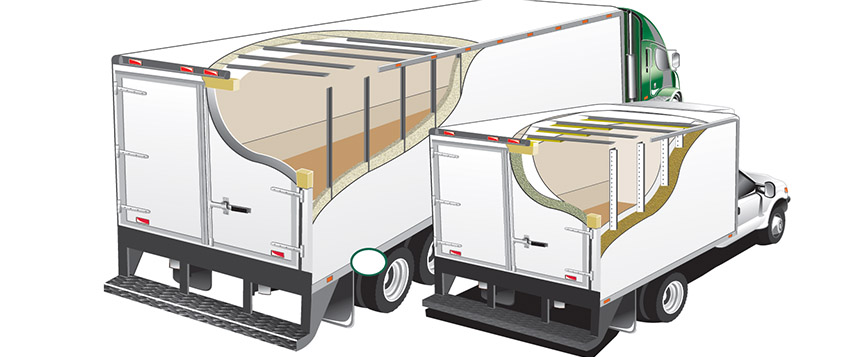
Staining Statement
Some staining/discoloration may occur to frp liner panels after they have been in service for several years. This is a normal wear condition. As long as acceptable cleaning methods (i.e.,
steam cleaning) are used, the surface should remain sanitary and acceptable.
Storage Requirement
Crane Composites panels are designed for peak performance prior to and after the panels have been applied. Careful handling during the manufacturing process is important. Avoid excessive clamping, dropping and scraping. Keep contents dry. Store indoors in a well ventilated area. When outside storage is necessary, cover and protect from the weather and exposure to sunlight.