Almost 50 years since the first moon landing, we continue to add, each and every day, to a legacy of buildings that risk the health of their occupants, but condensation does not make headline news.
Discussions about condensation often focus on insulation, sarking and ventilation, but the new requirements of Parts F6 and 3.8.7 of the NCC 2019 rightly can be found under the Health and Amenity headings of the new code.
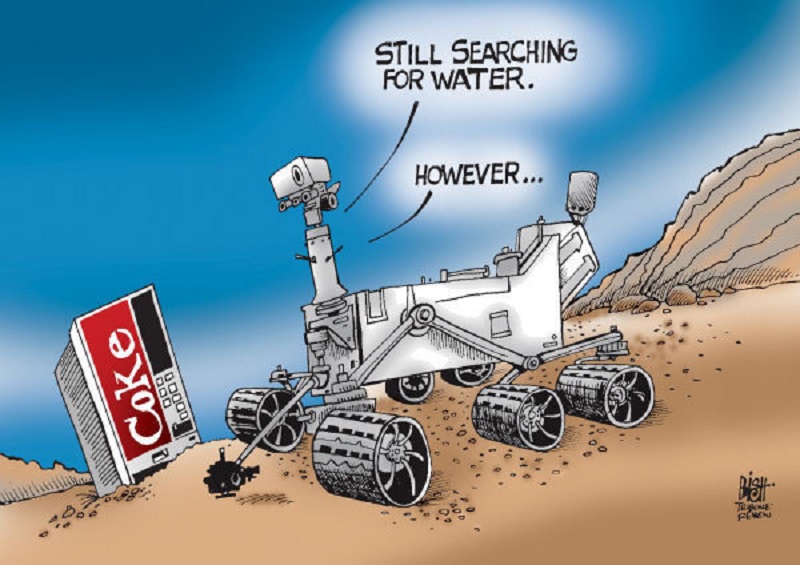
As occupants of damp and mouldy buildings are aware, the indoor environmental quality (IEQ) where Australians spend on average 90% of our lives, has a huge impact on our health, our quality of life, the demands on our public health system, and learning outcomes from our education system.
The Australian Building Codes Board (ABCB) conducted in 2015 a Scoping Study of Condensation in Residential Buildings. The report was completed in September 2016 but it took a further year before the frightening, but not unexpected findings were made public by the ABCB.
“Based on the nationwide condensation survey, more than 40% of new buildings have condensation and mould.” [1]
The amount of moisture trapped within buildings has been linked to compromised structural systems, loss of inbuilt fabric durability, financial hardship to occupants, family breakdown and significant chronic diseases like asthma and other allergy and immunology conditions.
The report also found that costs associated with the long-term human health implications from condensation and mould within buildings, far outweigh the costs to implement regulatory, design, construction practice, and material choice changes.
At a recent launch event of the new code, the ABCB indicated the introduction of condensation management to the NCC was not a “magic cure,” that measures were only “a minimum standard” and indicated that quite likely, more changes will be introduced in 2022.
The new deemed to satisfy requirements are still limited in scope and can be summarised as:
- a requirement in cool and temperate climate zones 6, 7 & 8 that sarking must be vapour permeable to improve the chances of vapour safely escaping the building envelope.
- a requirement for ventilation of the roof space, if for some unforeseen reason there is a need or desire to have exhaust ventilation discharge into the roof space.
- requirements for minimum flow rates for exhausts in high moisture zones such as bathrooms, kitchens and laundries.
That such commonsense requirements need introducing to a mandatory code in 2019 is in itself a damning indictment about what is currently being built by some. For most good designers, the hurdle is so low that meeting these requirements will be easy, but that is no reason for complacency. The next phase of the code can’t come soon enough if we are to make any serious inroads to resolving condensation related problems in our buildings.
Windows are part of the solution
Condensation seen in the built environment is almost always a result of one or a combination of three circumstances:
- the presence of moisture levels which are too high;
- the presence of temperatures in the building fabric which are too low; and
- uncontrolled flow of water vapour from a source to a region of cold temperature (cold condensing surface).
The most familiar condensing surfaces in a building are windows. Window frames and glazing can be cold impermeable surfaces, exposed to high levels of indoor humidity and where condensation is also clearly visible to occupants. Condensation can be mitigated here by using double glazing and thermally broken window frames to keep the surface temperature above indoor dew point.
Seeing condensation on windows is a useful warning sign that more sinister and damaging condensation could be occurring unseen within the wall, roof and floor elements of the building.
Windows play a key role in managing IEQ. The requirement for operable windows to account for 5% of the floor area should, if opened, provide natural ventilation that replaces or dilutes polluted indoor air. Outdoor air typically has lower absolute humidity than indoor air so the opening of operable windows will also work to reduce indoor moisture levels.
Unfortunately for many valid reasons such as security, noise and cold drafts, windows are not opened, leading to a build-up of indoor air pollution and high moisture levels contributing to condensation issues. The mechanical ventilation code requires for the provision of makeup air to replace air exhausted from the laundry, kitchen and bathrooms. This can be provided by trickle ventilators such as AWS Ventient™ incorporated into the window, providing for outdoor air all day, every day, even when windows remain closed.
With innovations such as AWS Ventient™, a greater level of understanding across the industry, an acceleration of mandatory regulation and probably a few more court cases, we might even solve the majority of issues before we land on Mars.
More info download our brochure
Written by: Andy Russell of Proctor Group Australia
Dewsbury M, Law T, Potgieter J, Fitz-Gerald D, McComish B, Chandler T and Soudan A. “Scoping study of condensation in residential buildings – Final report” Australian Building Codes Board; Department of Industry Innovation and Science, University of Tasmania, September 2016.
Great work Andy